From autogenous welding through MIG/MAG to TIG welding – your partner for quality welded joints
Welding has been in industrial use since the end of the 19th century. Since then, various different disciplines have developed within it, such as MAG, MIG, WIG, MMA, Plasma, SAW, autogenous and laser welding. Using these welding techniques is accompanied by risks. Here at TÜV NORD we are a competent partner, supporting manufacturers and operators in the efficient implementation of daily welding tasks. Together with our customers, we develop approaches and solutions for their special welding challenges. Certified manufacturers of welded structures can be found in practically every sphere of life: without welding there would be no machinery, pipelines, steel structures, vehicles, aeroplanes and ships; even some medical products require this process.
Our services are intended for:
- The manufacturers and operators of welded structures (e.g. apparatus and containers, pipelines, steelwork, machinery, railways, defence)
- Engineering firms
- Manufacturers of filler metals
- Suppliers of fillers and welding equipment
- Steel traders
- Machining and cutting companies
- Welder training facilities
- Recruitment agencies
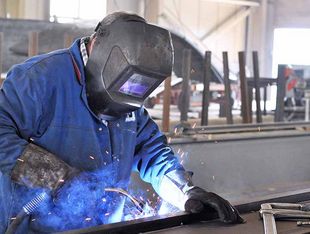
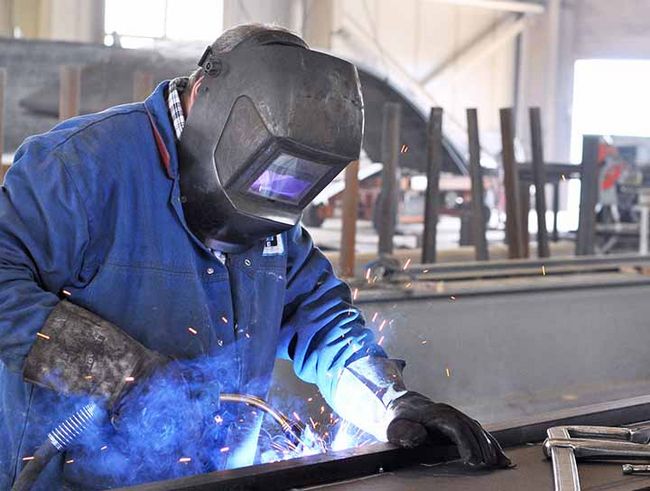
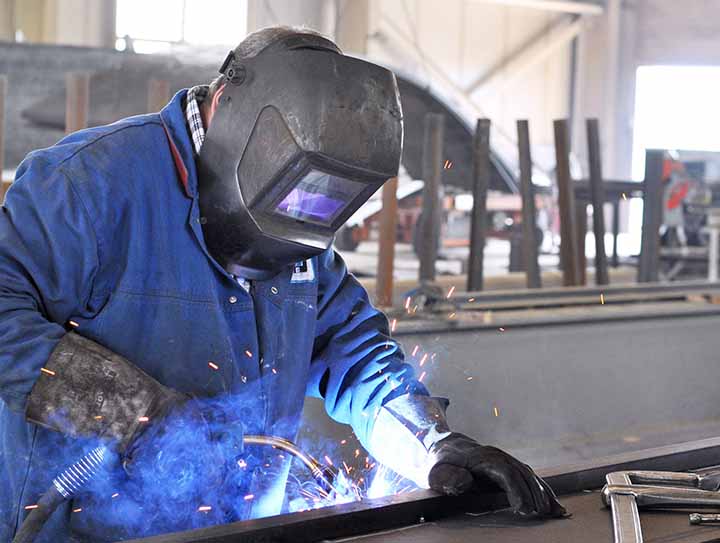
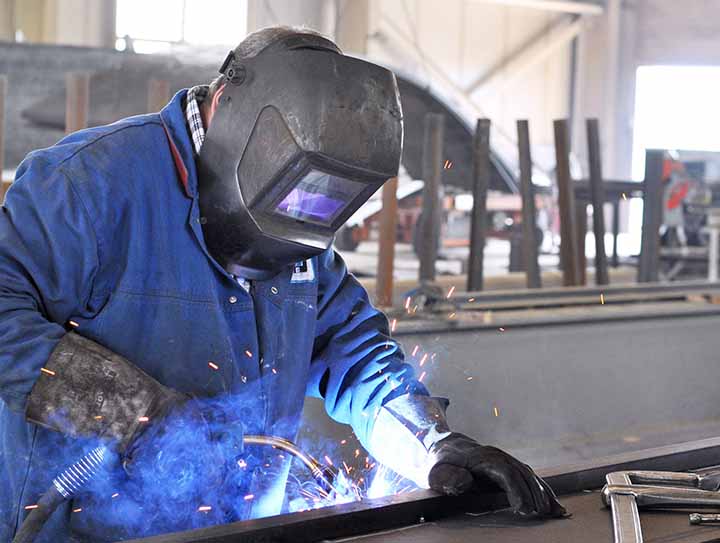
The right personnel qualifications for welding
For the manufacturers of welded steel structures and pressure vessels, rails and defensive technologies, the expertise of the staff that work on them is of decisive importance. With a recognised TÜV NORD certification, welding operations can, in accordance with their obligations, document and communicate the capabilities of their employees. This is an important factor in convincing demanding clients and fulfilling stringent regulations. The qualification of your employees in the field of welding will be carried out by the inspectors at TÜV NORD as a “notified body” in accordance with all the current rules and regulations. This means you can be absolutely assured of the expertise and suitability of, say, your welders, testers and quality assurance/quality management system operators. To keep your knowledge up to date, we organise regular seminars, training measures and courses.
- Safeguarding personnel qualifications
- Support for all welding tasks as regards certification of welders, e.g. welding exams to DIN EN ISO 9606, DIN EN ISO 14732, DIN EN ISO 17660 and soldering exams to DIN EN ISO 13585.
- Specialist support from experienced welding technicians or International / European Welding Engineers/Inspectors (IWE/EWE/EWI), additionally qualified to DIN EN ISO 9712
- Information on current regulations and requirements and answers to legal questions relating to qualification
- Manufacturer qualifications and welding process and personnel qualifications all from a single source
- Recognised as a “notified body” for the certification of welders
- Extensive experience gained from national and international projects
- Accreditation as a neutral testing organisation
- Always on top of the latest regulations at home and abroad
- Fast reaction times
- Strong regional presence
- Proven expertise of your employees
- TÜV NORD certification recognised worldwide
- Training measures for your employees
Safeguarding welding tasks with process qualifications
Construction in steel by specialist companies allows the creation of demanding structures for buildings, halls, roofs, bridges, cranes and other edifices. For companies that carry out these complex tasks, along side the required manufacturer qualifications to DIN EN 1090, legally watertight documentation of processes is also of great importance. The same applies to manufacturers of pressure equipment to the Pressure Equipment Directive (2014/68 EU) and the suppliers and manufacturers of railway and defence products (DIN EN 15085 and DIN 2303). With a neutral, recognised confirmation by TÜV NORD, welding operations are in safe hands here. Process qualification for joining processes The WPQR (Welding Procedure Qualification Record), created in collaboration with recognised materials testing laboratories, safeguards the documentation. These separation and joining processes can be certified to German, European and international requirements and regulations. TÜV NORD has the recognition required to qualify your processes. In addition, our over 100 years of experience allow us to offer further services for all welding-related tasks, making us a competent contact for all questions relating to legal matters and regulations.
- Safeguarding process qualifications for joining processes (WPQR)
- Specialist support from experienced welding technicians or International / European Welding Engineers/Inspectors (IWE/EWE/EWI), additionally qualified to DIN EN ISO 9712
- Confirmation of safe, reproducible work processes to AD 2000-HP 2/1, DIN EN ISO 3834, DIN EN 1090-2, DIN EN 15085, DIN 2303 and other standards
- Support for all welding tasks
- Information on current regulatory amendments and legal questions
- Manufacturer qualifications and welding process and personnel qualifications all from a single source
- Recognised as a “notified body” for the certification of welders
- Extensive experience gained from national and international projects
- Accreditation as a neutral testing organisation
- Always on top of the latest regulations at home and abroad
- Fast reaction times
- Strong regional presence
- Proven expertise of your employees
- TÜV NORD certification recognised worldwide
- Training measures for your employees
Reliable structures thanks to documented manufacturer qualifications
Welded structures are subject, as a rule, to European guidelines and international standards. For example, the European Construction Products Directive (305/2011 EU) demands, via DIN EN 1090-1, that construction products with a CE label can only be brought to market by companies that have been inspected and certified by a notified body such as TÜV NORD. The standards are not the same for every company here: depending on the type of structure to be welded, the extent of potential damage, the material used and other criteria, four execution classes (EXC 1 to EXC 4) are used. In the welding of railway vehicles and their components to DIN EN 15085, the standard divides manufacturers and the parts they weld into three tiers, CL1 to CL3, depending on the safety function of the welded part. The quality requirements for the manufacturers and maintainers of defence products are subdivided by DIN 2303 into quality classes Q1 – Q4. This in turn depends on the component classes BK1 to BK4. Manufacturer qualification in fields governed by the Pressure Equipment Directive (2014/68 EU), for example, taking account of AD 2000 leaflet HP0 or the standard series DIN EN 13445 and DIN EN 13480 also demonstrates that your products have left your factory in a quality-assured state. The basis for this and other product standards is DIN EN ISO 3834. In this “high-level norm”, the quality requirements for the fusion welding of metallic materials are described. TÜV NORD has all the necessary accreditation to carry out manufacturer qualification in the above fields. The TÜV NORD certificate enjoys worldwide recognition and will help you gain new customers.
- Verification documents (also as a combo audit as part of a QMS to DIN EN ISO 9001)
- Support for all welding tasks
- Expert in current regulatory amendments and legal questions
- Extensive experience gained from national and international projects
- Always on top of the latest regulations at home and abroad
- High availability and regional flexibility
- Reliable work certificates for engineering offices regarding conformity as per DIN EN 1090-1
- Competitive advantages for engineering offices taking on regular assessment tasks
- Optimisation of adjustment and production costs for manufacturing operations
- Closed quality provision chain as per DIN EN 1090
- Controlled manufacturing process to DIN EN 1090-1
- Comprehensive project support, all from a single source
We help with construction, assembly and manufacture, and with corrosion protection
- Solutions for long-term serviceability
- Comparison between the performance specification and declaration
- Safeguarding our customers and their customers
- Confirming processes
- Documenting the delivered quality
- Proof of the required or applied corrosion protection
- Protection against potential claims processes
- Assurance of quality-compliant component manufacture (national and international suppliers) in the form of supplier audits
- Design review (component specification, drawing and measurement assessment, draft inspection)
- Process validation (welding, inspection, goods receipt, quality assurance)
- Qualification of manufacturers of welded structures
- Training of welders
- Documentation (Digital, CAQ, BIMAS)
- Inspection of industrial coatings to DIN EN ISO 12944, NORSOK M501, ZTV-ING and individual project specifications or customer requirements (steel and plant construction, hydraulic steelwork, mechanical engineering, pressure equipment, railway vehicles)
- Monitoring, inspection and documentation as part of surface preparation and for organic or duplex coatings
- Inspection of hot-dip galvanised structures to DIN EN ISO 1461, DIN EN ISO 14713 and DASt guideline 022
- Creation and inspection of technical implementation documents and/or quality assurance documents
- Operational inspection, issuance of a “corrosion protection” certificate as a manufacturer qualification for the special manufacturing process as part of internal production control e.g. to DIN EN 1090
- Highly qualified experts, auditors and inspectors with key qualifications as international welding experts (IWE) to the DVS-IIW 1170 guideline and FROSIO-certified coating inspectors (Level III) to the Norwegian standard NS 47
- Accredited materials testing laboratories to ISO/IEC 17025 for the execution of diverse corrosion tests to national and international standards such as DIN, EN, ISO, ASTM, NACE etc.
- Increased quality
- Binding statements on conformity and performance data
- Professional, independent assessment
- The highest level of safety and quality
- Improved durability of your products
- Reduction of warranty claims
- Audited suppliers fulfil high demands of quality, manufacturing processes and personnel
- Competitive advantage thanks to certified manufacturing quality
- Safeguarding your success